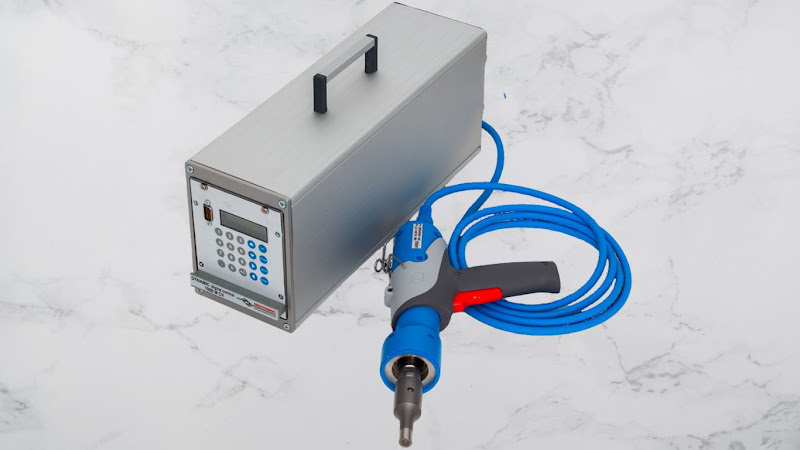
Ultrasonic welding, a strategy that uses high-repeat ultrasonic vibrations to make solid state welds between materials, has transformed into an irrefutably fundamental part in present day motorization. This cycle, which requires no concretes, screws, or fixing materials, offers different benefits for collecting and assembling exercises across various organizations. From auto to equipment, the mix of ultrasonic welding into modernized systems has changed creation processes, inciting overhauled efficiency, precision, and cost-feasibility.
The Basics of Ultrasonic Welding
Ultrasonic welding works by applying high-repeat vibrations to the surfaces of materials to be joined. These vibrations make heat through contact, which causes the materials to unwind and interweave. The cycle is fast, regularly requiring two or three minutes, and is significantly reliable, conveying strong and consistent welds. The deficiency of external force sources and additional materials makes ultrasonic welding an innocuous to the environment and energy-capable methodology. Crucial to this cycle is the ultrasonic machine, which expects a fundamental part in conveying careful and controlled vibrations for ideal weld quality.
How Ultrasonic Welding Further develops Capability in Current Motorization
Speed and Precision: One of the primary advantages of ultrasonic welding is its speed. The cycle can be done immediately, generally diminishing creation process lengths. The ultrasonic machine is intended to convey precise vibrations, ensuring that each weld is unsurprising and meets the important points of interest. This exactness is fundamental in organizations where part genuineness and consistency are head.
Cost Decline: Ultrasonic welding reduces the prerequisite for consumables like pastes, screws, or other connecting materials. This decline in material use prompts direct cost save reserves. Also, the speedy thought of the communication infers that less energy is consumed, further driving down practical costs.
Chipped away at Quality Control: In automated conditions, staying aware of consistent quality across enormous volumes of creation is principal. Ultrasonic welding is extraordinarily controllable, with limits like repeat, adequacy, and pressure actually mobile. This control ensures that each weld meets the fundamental subtleties, reducing the likelihood of deformations and adjust.
Comparability with Various Materials: Ultrasonic welding is adaptable and can be used on a large number of materials, including plastics, metals, and, shockingly, a couple of composites. This flexibility makes it an ideal choice for undertakings that work with various materials, ensuring that a comparable welding development can be applied across different item contributions.
Regular Benefits: The ultrasonic welding process is cleaner than various traditional welding procedures, as it doesn't convey exhaust, shimmers, or hazardous waste. In addition, the removal of pastes and other compound holding experts lessens the natural impact of the collecting framework.
Usages of Ultrasonic Welding in Current Motorization
Vehicle Industry: Ultrasonic welding is used extensively in the vehicle region for social event plastic parts, wiring harnesses, and, shockingly, metal parts. The speed and trustworthiness of the cycle make it ideal for high-volume creation lines.
Equipment Gathering: In devices, ultrasonic welding is used to make relationship between delicate parts without hurting them. This application is particularly huge for gathering printed circuit sheets (PCBs) and other delicate electronic contraptions.
Clinical Device Creation: Ultrasonic welding is used in the clinical field to assemble contraptions like catheters, channels, and cautious instruments. The cycle ensures spotless and solid joints, which are fundamental in clinical applications.
Packaging Industry: Ultrasonic welding is in like manner for the most part used in packaging, particularly for fixing plastic films and making impervious groups. This application is principal in the food and medication organizations, where thing genuineness and security are imperative.
Troubles and Examinations
While ultrasonic welding offers many benefits, there are a couple incites and thoughts to recall. For instance, the fundamental game plan cost for ultrasonic welding equipment can be high, particularly for custom applications. Additionally, the collaboration requires precise control of limits, and directors ought to be ready to get a handle on the intricacies of ultrasonic welding. Regardless, the somewhat long advantages, as extended capability and cost venture reserves, every now and again offset these fundamental troubles.
FAQs
Q1: What materials can be welded using ultrasonic welding?
Ultrasonic welding is suitable with an enormous number of materials, including thermoplastics, metals (like aluminum and copper), and a couple of composites. In any case, the materials ought to have relative condensing centers to achieve serious solid areas for a.
Q2: How does ultrasonic welding diverge from regular welding methodologies?
Ultrasonic welding is faster, more spotless, and every now and again more energy-capable than standard welding procedures. It doesn't require additional materials like fix or pastes and makes no exhaust or lights, making it safer for executives and the environment.
Q3: Is ultrasonic welding sensible for an extensive variety of present day computerization?
Ultrasonic welding is significantly adaptable and can be composed into various robotized systems. Nevertheless, its sensibility depends upon the specific application, materials being used, and the best outcome. Conversing with a specialist can help with choosing the best system for a particular undertaking.
End
Ultrasonic welding has basically impacted the efficiency of current computerization by offering a speedy, careful, and innocuous to the environment reply for joining materials. Its adaptability and ability to convey brilliant welds make it an extremely valuable gadget in present day creating processes. As organizations continue to search for approaches to smoothing out creation and decrease costs, the occupation of ultrasonic welding in current robotization is set to grow significantly further.